3D vision to help palletise parts with precision in the automotive industry
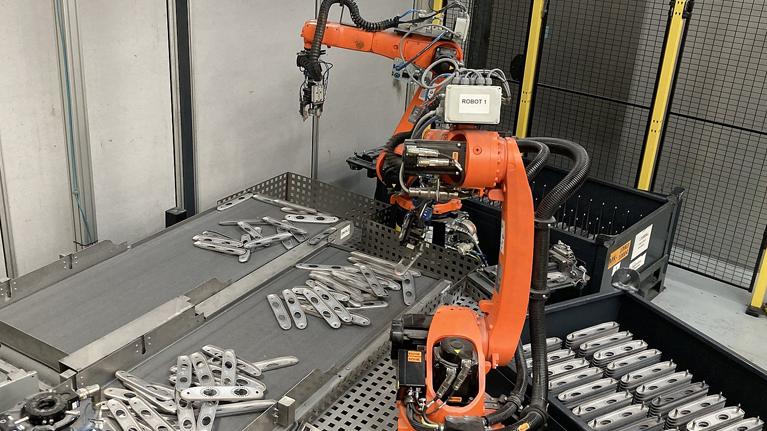
Tekniker has developed for the Cikautxo Group an innovative robotic solution for handling and transferring automotive components from one container to another.
The automation of palletising processes in industrial production is a great technical challenge due to the variety of geometric shapes and the chaotic positioning of the parts to be handled. However, the development of new vision and artificial intelligence technologies is opening up new possibilities in this field.
An example of this is the innovative 3D vision system developed by the Tekniker technology centre, a member of the Basque Research and Technology Alliance (BRTA), highly specialised in technological solutions for automation and industrial robotics, for the Cikautxo Group, a national manufacturer of components for the automotive sector.
Specifically, Tekniker’s research team has developed a robotic system controlled by artificial vision software that allows the precise feeding of industrial components into a container.
The solution, consisting of two robots and a 3D scanner, ensures precise gripping of the parts and their orderly deposition in a container specially adapted to the characteristics of the parts for their subsequent incorporation into the production workflow.
“We have worked with a 3D vision technology called Surfaced-based Matching, which acts as an eye for the robots and helps them to reliably recognise the components and move them from one container to another at a speed of 8 seconds per part,” says Eneko Ugalde, director of Intelligent and Autonomous Systems at Tekniker.
This new system developed by the technology centre allows optimising and automating a process carried out manually by the Cikautxo Group until now, speeding up palletisation, saving on production costs and freeing up staff for more demanding tasks.
Precise location without collisions
The main challenge of the configuration carried out by Tekniker is that the robots need to accurately recognise the position and orientation of the components in three-dimensional space in order to pick them up and put them down safely.
For this purpose, a solution has been developed based on Tekniker’s technological asset called SMARTPICKING, which is able to accurately identify objects by analysing 3D data and using the surface model as well as the corresponding geometric information.
The result of the analysis obtained is a pose of the robot in which it is able to manipulate the pieces in a certain order.
This asset, developed by Tekniker, makes use of the HALCON libraries for point cloud management. These are machine vision libraries marketed by the German engineering company MVTec, which Tekniker has been able to incorporate as a certified partner for its use since 2023.
“Thanks to HALCON, we can automate and optimise the robotic palletising process from start to finish. The software offers a wealth of sophisticated machine vision tools that can be used to precisely locate the parts to be picked while avoiding collisions and ensuring a safe and smooth pick-and-place process,” explains Eneko Ugalde.