Automation and digitisation of production processes for a more inclusive industry
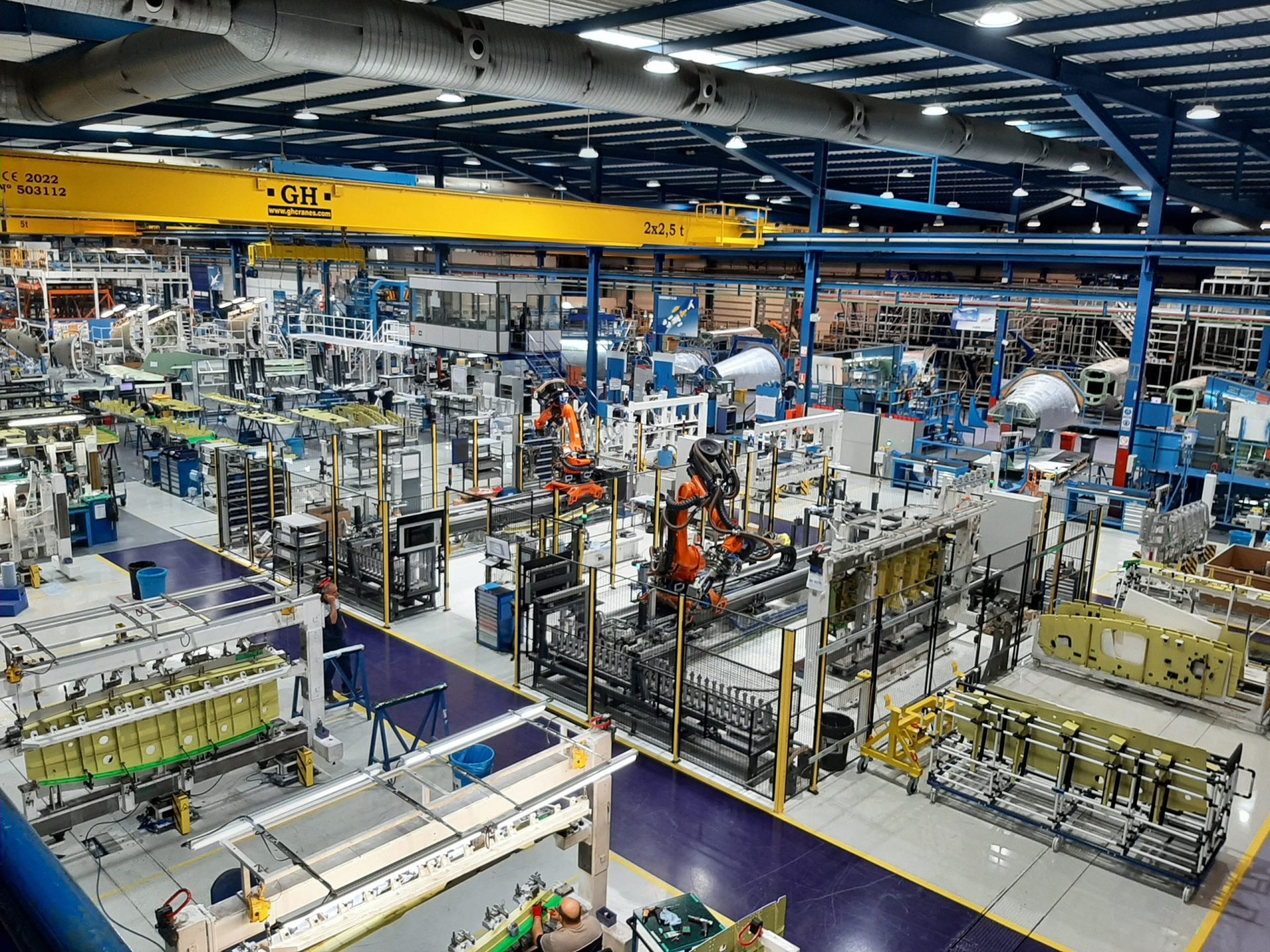
The Tekniker technology centre is participating in the European Masterly project through a case study that will be implemented in Aernnova’s production lines
The initiative will also test robotic innovations in the assembly of electrical cabinets for lifts and the automation of logistics in a Decathlon order warehouse
The transition towards a 4.0 manufacturing industry in which automation and digitalisation of production processes enable the challenges of sustainability, efficiency and profitability to be addressed is not equally easy for all companies, which has an impact on their competitiveness in an increasingly globalised market.
In this context, the technology centre Tekniker, a member of the Basque Research and Technology Alliance (BRTA), will participate from 2023 in the European Masterly project, which has as its main objective to support the technological advancement of SMEs and promote a wider and more inclusive adoption of technological and digital solutions.
To this end, a wide variety of flexible, intelligent and easy-to-use robotic systems will be developed by personnel to boost efficiency and innovation in industrial processes.
Specifically, Tekniker participates by providing technological solutions in the case study that will be carried out in Aernnova’s production lines to supply cutting-edge aeronautical structures.
During the initiative, the technology centre will be responsible for integrating automated assistance in the process of handling and loading of skins for the central box of the Airbus A220 and integrating various measurement sensors (force, dimensional) to monitor the assembly process of the central box.
Automation, monitoring and adaptation
The final demonstrator, which also involves the Technical University of Kiev, the German institute RWTH, the Greek company CASP and the Italian institute IIT, will, unlike existing robotic solutions, be able to handle a wide variety of parts of different sizes, shapes and materials with the aim of developing flexible and resilient production lines.
Modular grippers will be combined with smart technologies and cranes, and their control and sensing capabilities will be improved through artificial intelligence (AI).
At the same time, to speed up and increase the efficiency of the assembly of the aircraft structure, assembly will be carried out in a semi-automated environment with additional sensors to continuously monitor production, ensure part quality and provide workers with critical information to aid decision-making and anticipate errors or defects.
One of the keys to this innovation is that it will enable more autonomous and collaborative operation and, in turn, facilitate labour inclusion in the sector by offering tools and systems that adapt to the needs of the work environment and to any individual.
As a result, it is expected to improve the safety and comfort of personnel operating on the production line, as well as increase the accuracy and efficiency of the manufacturing process, enabling more competitive production.
In addition to the use case in the aeronautics sector, the Masterly project includes two other demonstrators: the assembly of electrical cabinets at the industrial manufacturer Kleemann, in which force control solutions will be developed for the assembly of different elements, and the automation of logistics in an order warehouse of the company Decathlon, integrating more flexible strategies.
With the participation of a total of 16 European partners, this initiative, which will end in 2026, is funded by the European Union’s Horizon Europe programme and is coordinated by the Laboratory for Manufacturing Systems & Automation (LMS) in Greece.