DIGITAL TWINS, A KEY ELEMENT TO OBTAIN SELF-CALIBRATING MACHINES AND ROBOTS
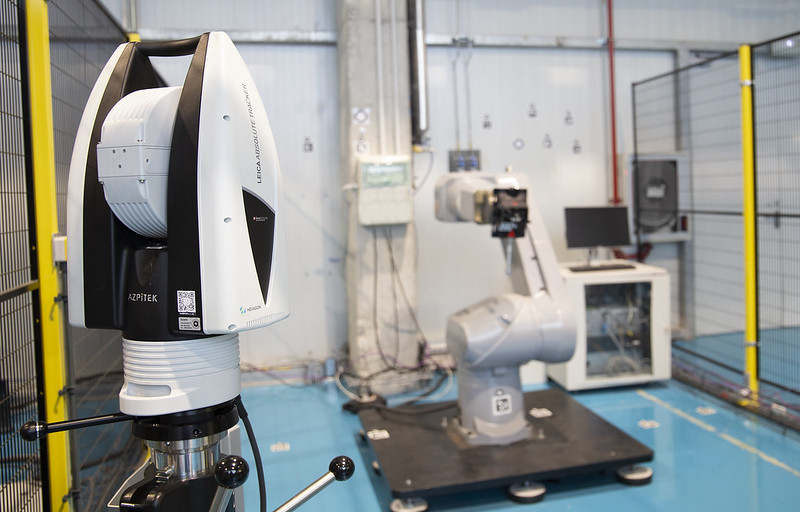
Tekniker has led the Precitek project to address the challenge of incorporating new digital solutions to production resources to advance towards a smart industry
Bigger industrial components, the application of new materials or the need to speed up production to respond to larger order intakes require new solutions to upgrade the performance of production equipment in environments that are becoming increasingly automated.
The Tekniker technology centre has led the Precitek project to meet the challenge of developing more accurate robots and machine tools by using advanced technologies such as digital twins.
Tekniker’s Precision Engineering and Industrial Metrology unit has managed to implement automatic self-calibration for equipment of this kind to minimise errors and advance towards a smart and resilient industry by using the virtual commissioning concept.
Virtual commissioning consists in fine-tuning an industrial handling or production system based on virtual simulations and critical information obtained in the operations performed.
Gorka Kortaberria, the researcher in charge of the project, explains that “we have tried to minimise the amount of time required as well as the costs associated with configuring machines and measurement processes. Another goal consists in being able to make adjustments in an agile and automatic manner based on production adaptation needs such as, for example, the need to manufacture new references.
Handling and manufacturing
It is within the framework of this initiative that Tekniker has developed and installed its self-calibration solutions on two technological demonstrators: a robot for industrial handling processes and a machine tool used for manufacturing.
The first solution was jointly developed with the Ideko technology centre and made it possible to speed up the robot’s calibration with integrated resources meaning that instead of taking 1-2 hours (in the case of off-line calibration) this could be done in approximately 15-20 minutes. It will also be possible to improve the precision range ten-fold, i.e., from 1-2 mm to 0.2-0.3 mm.
This system combines advanced photogrammetry strategies based on artificial vision systems, geometric patterns and kinematic models of the robot. Calibration and compensation procedures allow robots to be used in handling and manufacturing operations that are much more demanding such as insertion and measurement applications or ancillary operations for which accurate positioning is critical.
In the specific case of production resources, the initiative has focused on a very large machine tool, a piece of equipment for which it is crucial to improve precision and maintain this condition over time. It is also an enabler to carry out complex production processes.
In this instance, calibration has materialised by installing a laser tracker on the header of the machine and by automatically measuring the volume and geometry of the equipment. When managed from a user interface, the process can be carried out swiftly, in less than 30 minutes and compile the results obtained at a later stage.
Tekniker’s work has focused on modelling and characterising the machine’s behaviour so it can be used to perform demanding manufacturing processes, such as traceable measuring operations, i.e., so that the machine will not only be able to manage the manufacturing process but also possess sufficient capacity to control the quality of parts in an integrated manner.
The Precitek project, funded by the Elkartek programme sponsored by the Basque Government (2021-2022), has been led by Tekniker with the support of Ideko, Vicomtech, Tecnalia, IMH Campus and UPV/EHU.