Flying greener: TOSCA paves the way to sustainable aircraft
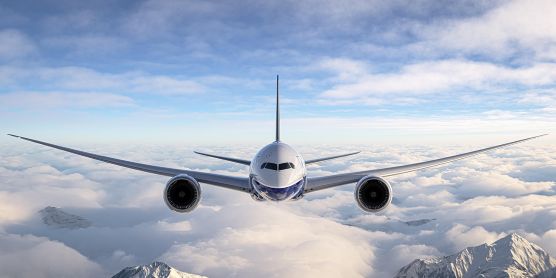
CIDETEC Surface Engineering boosts circular composites with high thermal stability vitrimers thanks to European collaboration
Aviation is about to undergo a major transformation: the European research project TOSCA is opening up new ways to make aircraft more environmentally friendly. The aim is to develop sustainable processes that improve both the efficiency of the production of high-tech materials – so-called composites – and their recyclability. These materials are essential for making lighter and more fuel-efficient aircraft. With a budget of more than €4.5 million from the Horizon Europe programme, TOSCA brings together leading research institutions and industrial partners. By 2027, they aim to develop solutions that help reduce the environmental footprint of aviation, an important step towards more climate-friendly flight for all.
The challenge: recycling composites in the aerospace industry
Fibre-reinforced composites are essential for lightweight, fuel-efficient aircraft, but recycling them remains a major challenge. Currently, less than 15% of composite materials are recycled; the rest is landfilled or incinerated. There are also unresolved challenges at the production stage: established processes often generate more waste than useful material. As carbon fibre composites are derived from petroleum-based precursors, unused waste translates directly into additional CO₂ emissions each year. As the aerospace industry moves towards greater sustainability, new technologies are needed to address these shortcomings without compromising high performance.
Innovative solutions: a smarter, more sustainable process chain
TOSCA aims to develop a new processing chain for composites made from glassimeric epoxy resin, a new-generation material that maintains the strength and durability of traditional composites, but significantly improves their recyclability. Unlike conventional resins, which harden permanently after curing, glassimeric resin can be softened again by applying heat and pressure, facilitating quick repairs and extending the life cycle of components. At the end of their useful life, these materials can be safely chemically recycled or reformed for other uses, laying the foundations for a truly circular composite economy. The project will also develop a highly automated manufacturing chain adapted to these new composite materials. By incorporating integrated inspection systems, which will allow automated quality control and digital process monitoring, the aim is to achieve defect-free manufacturing, optimising the use of materials.
Partner contributions: a collaborative effort towards sustainability
The TOSCA project brings together leading research institutions and industrial partners from across Europe, each contributing their expertise to address challenges in composite manufacturing and recycling. PROFACTOR, as project coordinator and technology provider, is leading efforts in automation, artificial intelligence-driven inspection and digitisation, to develop smart manufacturing processes that improve quality, efficiency and sustainability.
CIDETEC Surface Engineering will formulate and develop an advanced glassimetric epoxy resin with high thermal stability. This innovative material will significantly improve the repairability and recyclability of composites, while maintaining the mechanical strength and durability of conventional composites. CIDETEC’s contribution is crucial to enable a circular approach to the use of composites, aligning high performance requirements with sustainability goals.
The other partners – GMI Aero (France), FIDAMC (Spain), AIMEN (Spain), ITA (Spain), ÉireComposites (Ireland) and Addcomposites (Finland) – provide expertise in their respective areas to ensure the success of TOSCA. By the end of the project, the TOSCA consortium expects to have developed a sustainable and fully optimised manufacturing process that will shape the future of aerospace composites: reducing waste, reducing emissions and increasing Europe’s strategic autonomy in advanced materials.