GAIKER, together with Petronor and Zorroza Gestión obtain pyrolysis oils from plastic waste
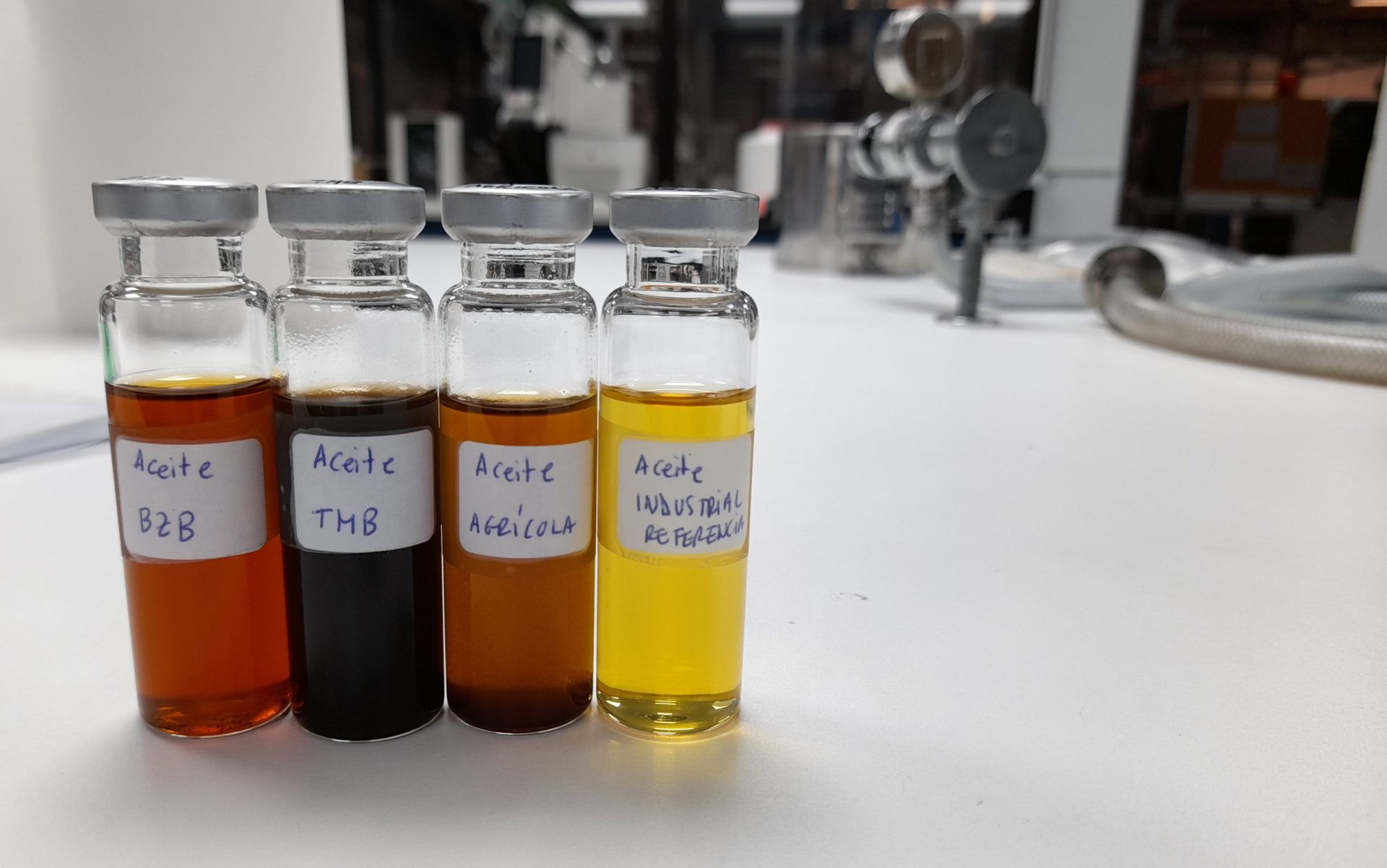
With the Plastic2Plastic project, pyrolysis oils have been obtained from plastic waste for use as a raw material in the refinery sector and in the petrochemical industry.
The Plastic2Plastic project in which the GAIKER Technology Centre, a member of the Basque Research & Technology Alliance, BRTA, together with the companies Zorroza Gestión S.L., leader of the project, and Petronor, have participated, has come to an end with satisfactory results.
Plastic2Plastic began in 2021 with the aim of obtaining pyrolysis oils of sufficient quality for the manufacture of new products from plastic waste that was destined for landfill. In this way, a second life would be given to this waste and savings would be made in raw materials and energy.
This was a continuity project, as GAIKER and PETRONOR had also been working on the REQUIPLAST project in which they had studied the use of reject flows, with a high plastic content, to obtain oils with a homogeneous and controlled composition by means of the pyrolysis process.
This new research, financed by the Basque Government’s Public Company for Environmental Management, Ihobe, as part of its circular eco-innovation aid programme, has further developed some of the key aspects previously identified in REQUIPLAST, such as:
- The preparation and conditioning of waste for the subsequent pyrolysis process based on composition and morphology criteria.
- The development of a robust and simple process that operates at moderate temperature and pressure conditions and allows high yields of pyrolysis oils of a quality accepted by industrial pyrolysis oil conditioning facilities, for use as a subsequent material.
- Verification and control of the quality of the oils produced.
- The evaluation of the options for the material recovery of the by-products, such as the carbonaceous solid.
GAIKER has extensive experience in the development of processes for the chemical recycling of plastics, and also has a wide variety of separation and conditioning equipment and pilot plants for scaling up thermochemical pyrolysis processes. For this reason, in this project it has been in charge of both the definition of the waste separation and conditioning processes and the optimisation of the selective pyrolysis process. It has also analysed the pyrolysis oils and the carbonaceous product obtained in order to evaluate options for material recovery.