New technologies to speed up decarbonisation in the area of steel production
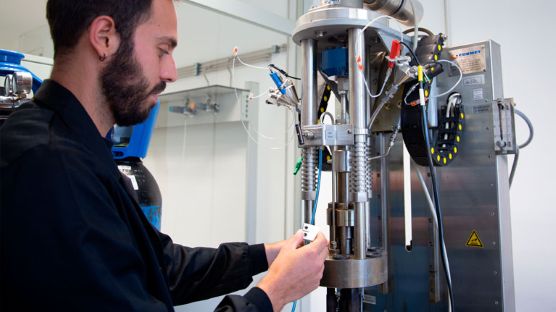
Tekniker is participating in MODHEATECH, a European project focused on developing an innovative heating system for furnaces at steelworks.
The global demand for energy in the area of steel production is mainly associated with fossil fuels. It is therefore not only essential to find and establish new formulas to reduce environmental impacts originating from the production of steel but also to meet the targets set by leading European and international administrations.
The Tekniker technology centre, a member of the Basque Research and Technology Alliance (BRTA), has collaborated with the European MODHEATECH project since its inception in 2023 to investigate a technological alternative that can address the specific challenge of decarbonising the steelmaking sector. The initiative specifically focuses on furnace heating processes currently in operation at steelworks that run on natural gas and produce significant environmental impacts.
Cristina Cerrillo, a Tekniker researcher, explains that “the project is developing a hybrid heating system that combines a number of technologies that will not only improve sustainability in the area of steel production but also achieve higher levels of energy efficiency and productivity”.
The ultimate goal is to deploy an optimum furnace heating technology based on partial electrification by the installation of an induction system and gas-burning properly combined, and the energy recovery of the off-gases from the furnace. Renewable energy sources and heat recovery systems will be used to produce the electricity required by this system.
Hydrogen and induction
It is within the scope of this project that Tekniker will use a virtual demonstrator operated by Sidenor to ascertain the impact and feasibility of using hydrogen combustion technologies and induction heating in steel production processes. An integral approach will be applied to the following: a life cycle analysis (environmental, social and economic) to choose optimum solutions; the definition of a predictive and proactive maintenance strategy; an analysis addressing critical components and the execution of accelerated tests under harsh conditions to ensure that hydrogen is compatible with the materials used in the facilities.
The initiative intends to reduce CO2 emissions by 20% and increase productivity without affecting the quality of the end product, use 50% of self-produced green energy to operate the system and define a roadmap to speed up decarbonisation in the sector.
The researcher underscores that “as induction heating produces zero direct emissions and efficiency exceeds 60%, it is much better than traditional gas-burning techniques whose efficiency peaks at about 30%”.
The technologies developed to date will also address waste reduction issues to improve the quality of products and facilitate independence from fossil fuels in EU countries.