‘SMART’ QUALITY INSPECTION TO ACHIEVE ‘ZERO DEFECT’ PRODUCTION
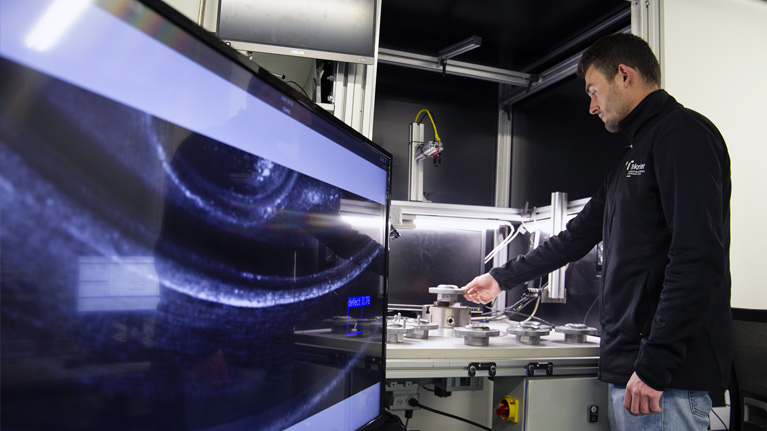
Tekniker has developed a real-time solution to automatically detect surface defects on automotive parts.
Quality control is becoming increasingly important for the production lines of industrial manufacturers. Stringent finishing requirements aimed at producing “zero defect” products, eliminating waste or avoiding product returns require innovative solutions to not only improve the efficacy of error inspection actions but also save money.
This need becomes even greater when, for instance, surface defects have to be spotted on auto parts but are usually very hard to see with the naked eye because they are faint when present in the form of scratches, marks produced by improper handling, pores or cracks. Although defects of this kind do not affect product performance, reality shows that complaints are filed, and auto parts are returned as a consequence.
In order to address this problematic issue, the Tekniker technology centre has collaborated to develop a real-time solution within the framework of the PILAR project to automatically detect surface defects on newly made parts before they reach the packaging stage.
The technology uses artificial vision and is supported by an AI model trained by Tekniker experts featuring a data base with 2D surface images, both with and without defects. The images have been labelled by a quality expert from Cikautxo currently involved in the project as an end user.
Eneko Ugalde, head of Tekniker’s Autonomous and Intelligent Systems Department, says that “the purpose of our system is to help and assist quality inspection operators to automatically and objectively reject parts showing signs of surface defects so that inspectors will only have to be called in case of doubt”.
90% reliability
One of the key actions required to improve the rate of success of the solution developed by the technology centre has consisted in compiling a large number of images showing different defects in several locations.
Eneko Ugalde also states that “we have used several techniques to increase the number of images in the data base and further their variability synthetically. Moreover, we have introduced genetic algorithms to establish the best combination of hyperparameters to enable the model to be trained”.
Subsequent to training the model, the technology centre’s research team implemented the system on a demonstrator test bench to perform real-time validation. The Tekniker expert explains that “we have obtained some very positive results and reliability now stands above 90%”.
The next step of the project is to analyse the possibility of pre-industrial validation: installing the unit developed on the production line to benchmark the solution under real production conditions.
The PILAR project ended in March 2023 and received funding from by the Basque Goverment’s Hazitek programme. One of the companies involved, among others, was the IDS Industrial a member of the consortium.