The WATEREYE project to reduce costs at offshore wind farms comes to a successful end
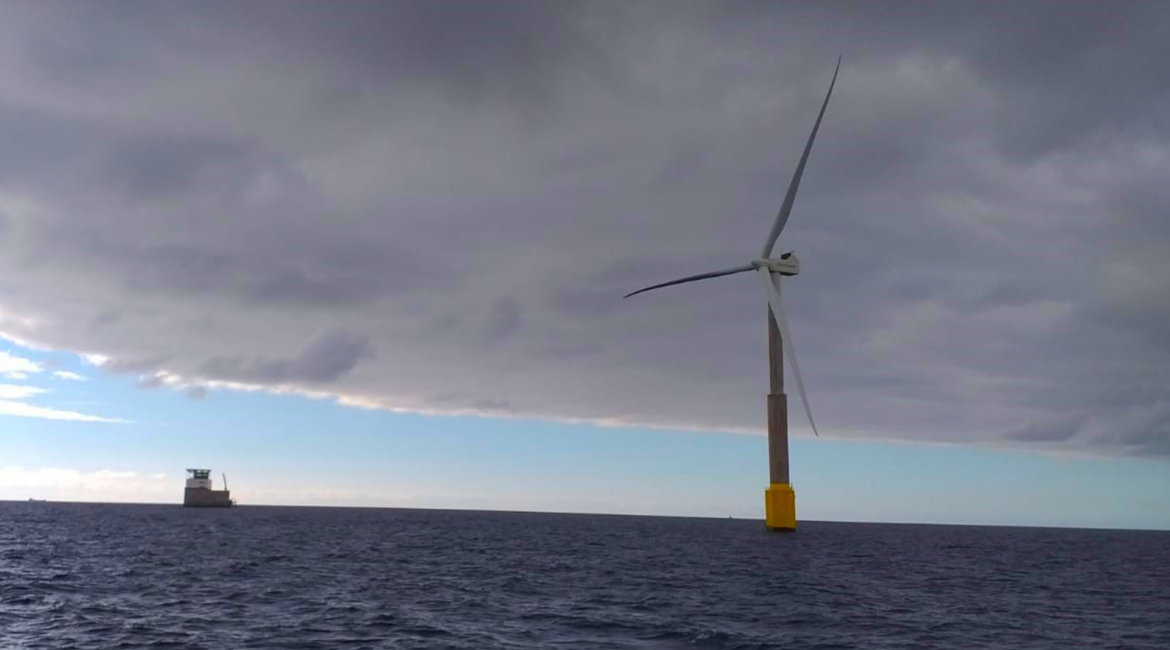
Corrosion is one of the main causes of faults in offshore structures, and one of the most serious if it occurs.
The WATEREYE project headed by the Ceit Technology Centre has been funded by €4.7 million from the HORIZON 2020 European Programme.
Over the past three years, the WATEREYE project has sought to create a significant impact on the functioning of offshore wind farms and their operation and maintenance costs – one of the major problems facing this sector.
Offshore wind energy is a very rapidly growing source of energy, owing to the fact that it provides stable high power to the grid and at highly competitive costs. Even so, one of the greatest problems facing this type of energy derives from the difficult access to wind turbines and to the complex environmental conditions at sea, which substantially increase operation and maintenance (O&M) costs over onshore wind farms. These costs can account for 30% of the levelized cost of energy for an offshore wind farm.
Specifically, corrosion is the root cause of high O&M costs and of faults in offshore structures, as it is less likely to be detected and is more serious in the case of such faults. Inadequate monitoring of corrosion protection and its inadequate management tend to result in deterioration of the supporting structures of offshore wind turbines. Moreover, the cost of repairs to the corrosion protection system can be far greater than the installation cost of that system itself.
The WATEREYE project was set in motion within this context as part of the EU’s HORIZON 2020 Research and Innovation Programme and funded by 4.7 million euros. The Ceit Technology centre has headed this 3 year project in which the following companies have taken part: Cobra (Spain), Semantic Web Company (Austria) and Delft Dynamics (Netherlands); the following R&D centres: Flanders Make (Belgium), Plocan (Spain) and Sintef (Norway); and the Technical University of Delft (Netherlands).
WATEREYE seeks to improve the functioning of offshore wind farms
The main aim of the WATEREYE project is to reduce operation and maintenance costs of offshore wind turbines, thus helping to improve the functioning of offshore wind farms via the remote monitoring of their structural health. To do so, a new real-time system has been proposed to monitor corrosion, which is a major problem in these types of offshore structure. “The system that’s been developed is based on ultrasounds and seeks to undertake continuous monitoring of the steel structure from inside the offshore wind turbine tower, where some sensor nodes that measure the thickness of the structure are deployed, and hence monitoring of any loss in thickness owing to the corrosion phenomenon”, Ceit researcher Ainhoa Cortés explains.
The technology is made up of fixed sensors and a drone-based mobile sensor node. This mobile solution, which Delft Dynamics has helped to develop, makes the ultrasound detection device fly to a specific point within the wind turbine tower in order to take the measurement. The drone, which cannot use a GPS inside the turbine, moves according to the information provided to it by a monitoring chamber combined with other position sensors as far as a series of critical points in the structure. This is where thickness is automatically measured by the ultrasound sensors developed by Ceit.
To develop this solution, Flanders Make was responsible for designing the 3D interface in order to display the state of the structure based on sensor measurements and the installation of a scale model of the wind turbine tower, in which a suitable environment was created to take the measurements.
For its part, Plocan has taken on the role of organising validation and final integration of the WATEREYE project at its installations – a unique place where technology can be tested in a real environment.
The project comes to a successful end after fulfilling its main challenges
Following three years of work, the WATEREYE project has come to a successful end, having fulfilled the main challenges facing it and seeing to make a significant impact on the functioning of offshore wind farms and their maintenance. Early, smart and accurate detection of any corrosion in the structures helps insurance costs, the effort involved in inspecting corrosion (linked to operation costs) and maintenance costs to be reduced, and availability is improved by incorporating data about corrosion.
The project is currently positioned at a TRL5 level of technological maturity, and it is hoped that the technology developed may be used in pilot projects over the coming months with a view to ensuring it is ready to be commercialised within 3 years.